This is an invite to Bay Area Vinyl lovers to come and hear our reference system and perhaps report their findings back to this forum. Specifically, to hear the new SW1X LPU III Balanced Phono Stage in this context…
Please contact me here joe@lotusgroupusa.com
May I humbly say that I believe you will find this to be a rewarding experience
(older photo - see below for current lineup)
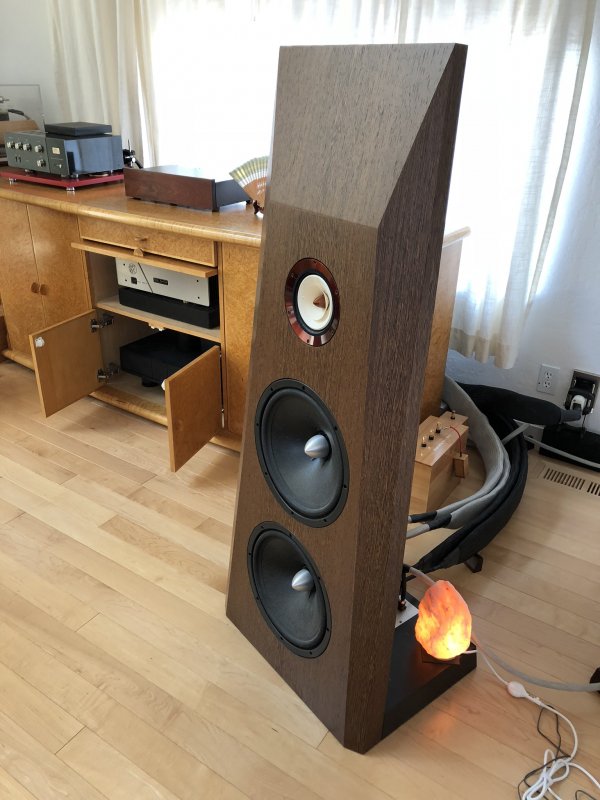
Components
Please contact me here joe@lotusgroupusa.com
May I humbly say that I believe you will find this to be a rewarding experience
(older photo - see below for current lineup)
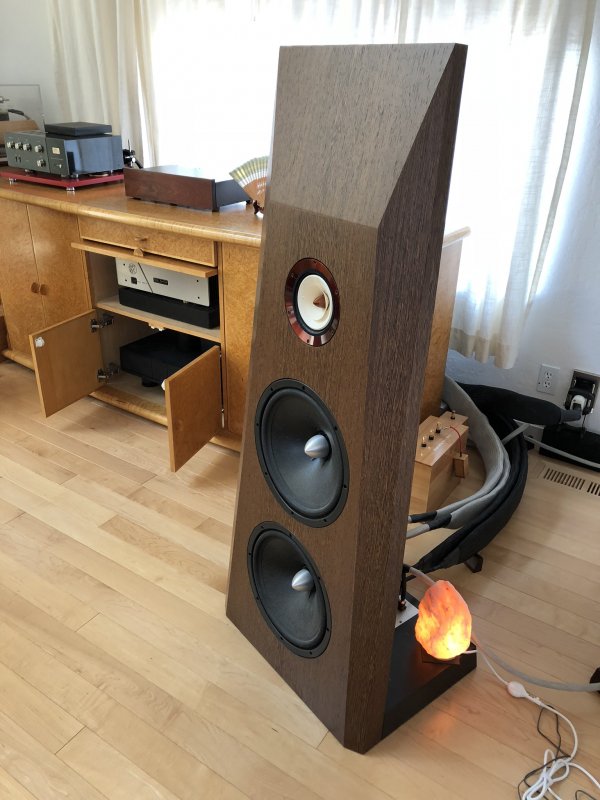
Components
- The Lotus Group Granada Loudspeaker with X1 Crossover 1 Pr
- Open Baffle Design
- 5" Feastrex D5e Type II Field Coil Drivers and Power Supply
- 2 - 12" Dual Voice Coil Woofers
- State of the Art Digital Crossover
- State of the Art Room Correction
- Frequency range 25hz to 20k
- Dimensions: 22" Wide, 54" Tall, 16" Deep
- Lotus Group built custom turntable with Redpoint Platter, bearing and motor pod
- Durand Kairos tonearm
- Ortofon Windfeld Cartridge
- EAR MC4 Step Up Transformer
- SW1X LPU III Balanced Phono Stage
- SW1X DAC III Balanced/Sony LCD-1
- Audio Note M3 Preamplifier
- SMc 125-watt Stereo Amplifier
- PranaWire Lalit Phono Cables (2)
- PranaWire Vajra Power Cables 1.5m (2)
- PranaWire Cosmos Power Cable Custom 1.5m (1)
- PranaWire Cosmos Power Cable 1.5m (1)
- PranaWire Sukhavati Power Cable 2.0m (1)
- PranaWire Avatar Speaker Cable 2.5m (Woofers) (1)
- PranaWire Sukhavati Speaker Cable 2.5m (Main Drivers) (1)
- PranaWire Arhat RCA IC 1.5m (1)
- PranaWire Sukhavati IC RCA 1.5m (1)
- PranaWire Sukhavati XLR IC 1.0m (1)
- Acoustic Revive RCP-1 Power Line Conditioner (2)
- Acoustic Revive RR-888 Ultra Low Frequency Generator (2) w/ Outboard Linear Power Supplies
- Q AB4045 Hybrid Ceramic Platforms (2)
- Q HEM-25 Footers - Sets of 4 (6)
- PranaWire Linebacker XE In-Line Passive Power Conditioners (2)
- PranaWire Sovereign Linebacker (2)
- PranaWire DanTien Footers Sets of 3 (3)
- Furutech NCF Boosters (6)
- Q TA-102 Damping Material (3)
- Q TA-32 Damping Material (1)
- Q IP-11 Cable Supports (4)