http://www.theabsolutesound.com/articles/von-schweikert-audio-ultra-9-loudspeaker/?page=2
Von Schweikert Audio Ultra 9 Loudspeaker
Revelation
by Greg Weaver | Nov 14th, 2019
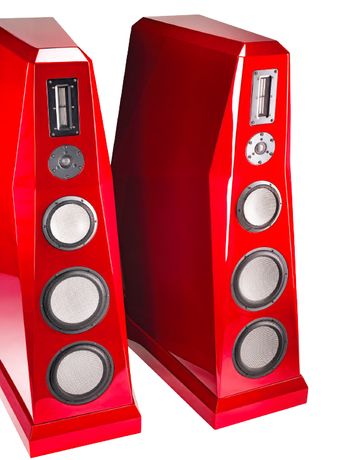
To understand the genesis of the new-generation VSA Ultra loudspeakers, we must go back to 2012, when a loyal, long-time VSA flagship owner contacted company founder Albert Von Schweikert and asked him to construct a one-of-a-kind, cost-no-object speaker. It will come as no surprise that Albert already had a theory for such a design, and this single project would overshadow everything, save standard production at VSA, for more than three years. Once Albert had settled on the drivers necessary for this ambitious project, Damon Von Schweikert, Albert’s son (and as of fall 2015 VSA’s CEO), spent a year on the enclosure alone. The overarching focus of this design was to reduce all forms of distortion, mechanical and electrical, to the lowest levels achievable. Even today, in any given system loudspeakers have the highest percentage of distortion of all components in the chain. (It’s unnerving to realize that even the most highly regarded speakers produce on the order of 3 to 5 percent distortion or more at their rated output.)
What would come to be known as the VR-111XS was housed in six separate enclosures, three per channel. Each channel included a nine-foot-tall concentric-array/line-source hybrid, housing eight magnesium 7" woofers, four magnesium 5" midrange drivers, two 1" horn-loaded magnesium dome tweeters, and an Air Motion Transformer super-tweeter, with an identical set of tweeters (two domes and an AMT), mounted in an ambient array on the rear baffle. The second nine-foot-tall tower housed four 12" magnesium subwoofers (with quad voice coils), each one powered by its own amplifier, while the third enclosure housed the impressive custom dividing network. All enclosures were fabricated with VSA’s proprietary “Triple-Wall Laminate Construction,” a unique constrained-layering technique utilizing three fundamentally different materials, each with vastly different “Q.”
The realization of this heroic loudspeaker would prove to be Albert’s swansong. As the finishing touches were being addressed in preparation for delivery and installation in mid-2015, he announced his retirement. This meant that Leif Swanson, Albert’s handpicked successor who has studied and worked with Albert for more than a decade, would assume the mantle of VSA’s head designer.
It was during the delivery and installation of this $750,000 statement design that Leif and Damon heard the VR-111XS in the customer’s purpose-built 25' by 75' by 16' room, and realized just how successful their three-and-a-half-year-long journey had been. Upon hearing how effectively they had achieved their desired goals with this speaker, the notion struck them both that they simply had to reimagine their entire flagship line. In November of 2015, the seed of what would become the Ultra line had germinated.
My impressions upon hearing the first speaker to result from this new initiative, the $300,000 Ultra 11 (which launched at AXPONA 2017), was that it represented a new benchmark, unmistakably surpassing the performance of every other speaker, regardless of price, that I had heard to that time. While some of the more competitive challengers offered remarkably diminished levels of distortion and perhaps even comparable degrees of resolution and transparency, in the areas of coherence, tone color, soundstaging, and especially dynamics the Ultra 11 simply had no equal.
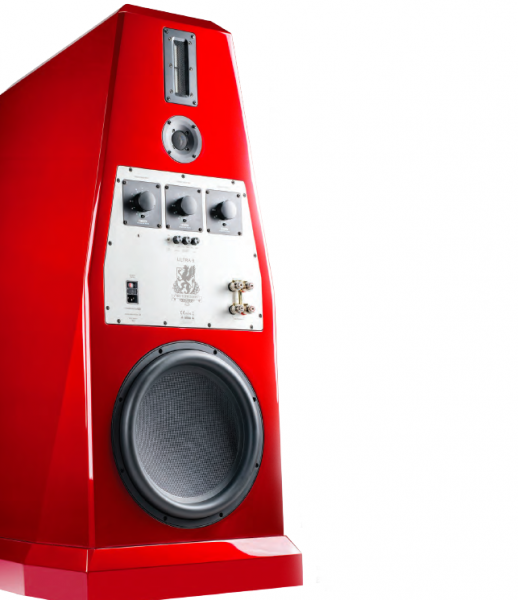
When I arrived at the Denver Marriott Tech Center before the opening of RMAF 2018, I was granted the singular privilege of getting a quick preview of the Ultra 9. What I had expected to find was simply a scaled-down version of the Ultra 11; after all, when comparing the two it is immediately apparent that the Ultra 9 is literally just the bottom half of an Ultra 11. But what I heard with the Ultra 9s being driven by Kevin Hayes’ then brand-new Valve Amplification Company Statement 450i iQ integrated amplifier (full review in progress) in this particular room and under the challenge of show conditions, was an entirely different, slightly more refined and involving speaker—one that in every way, save for the utter effortlessness and unrestricted dynamic scale of the Ultra 11, was as unfailingly authentic to the recorded event as its superb predecessor.
Getting in Tune
Seeing the Ultra 9 for the first time in its lustrous brilliant red finish is striking. Its multifaceted sides and angled front baffle give you the impression that it must be next to nightmarish to assemble. The fact that there are no right angles anywhere, nor any wider-than-necessary baffles to generate diffraction or interfere with dispersion, is also immediately evident. And weighing in at over 500 pounds and standing 50 inches tall, 32½ inches deep, with a 12-inch-wide front baffle (widening to a maximum width of 27 inches in the rear), this inspiring and massive device offers an amazingly streamlined and unimposing profile in every room where I have seen it installed, my own included. (My wife actually said, unprompted, “Those look amazing!”) Further, unlike many similarly sized speakers, the Ultra 9s are remarkably easily positioned on virtually any surface, with their rugged caster system, completely hidden by the purpose-built, form- and finish-matching skirt around the bottom of the enclosure.
The outermost layer of their proprietary triple-wall laminate composite enclosures consists of a sheet of resin-based HDF (high density fiberboard), a “medium” Q material, followed by a sheet of synthetic stone, fabricated from crushed gravel and various other minerals and a resin binder, with the third and innermost layer of hard felt (which has an extremely low “Q”), resulting in a wall some 4" thick. All three layers are bonded together using a layer (on the order of 1/5th of an inch), of industrial, anti-vibrational, plasticine-and-clay hybrid adhesive, integrating additional mechanical barriers capable of “shearing” energy by converting unwanted mechanical motion into heat for dissipation. Finally, using a method VSA has termed “Gradient Density Damping,” three different thicknesses of wool-like synthetic damping material are applied. Packed extremely tightly closest to the cabinet walls, the wool is gradually decreased in density as it nears the rear of the driver in its baffle, providing exceptional absorption while greatly reducing reflections back into the cone.
This inventive enclosure construction technique, known as “Aktive Cabinet Vibration Control, Version 2.0,” is the result of Albert’s extensive research using the California Institute of Technology’s (Caltech) Laser Interferometer Labs to study and measure speaker cabinet-wall vibration and the subsequent release of stored energy. It was pioneered and first applied in the original Von Schweikert Research VR-4, circa 1992.
While VSA readily acknowledges solid aluminum will be much more sonically inert than good ol’ HDF, they are quick to point out that this triple-walled, constrained-layer design results in sonic results measurably equivalent to and arguably even slightly more effective than milled aluminum. And it is radically more cost-effective. VSA feels that this method does not “squander” value, allowing the company to maximize the worth of the resultant product. This enclosure design technology has proven so successful that it is used in every VSA model in production today.
Lowest on the front baffle, the first two-thirds of which is swept back at about seven degrees, are two modified Accuton 8" honeycomb-ceramic drivers. Covering the 50 to 250Hz region and offering superbly flat response, they are fed from their fourth-order acoustical G.A.I.N. dividing network (more on that later). Though there is no low-frequency electrical filter, the explicit internal volume of the enclosure imposes a very steep acoustical roll-off below their lowest (50Hz) active frequency. Because they are not required to reproduce frequencies below 50Hz (there is a 15" subwoofer for that), these drivers exhibit an agility that results in both lower modulation and greater detail throughout their operational bandwidth.
Above the dual woofers, on that same swept-back section of baffle, is a unique Accuton 7" ceramic dome midrange. It implements an entirely new design approach Accuton calls the 4D (Direct Dome Drive Design) concept. As the spider is no longer connected to the former, its construction removes 15mm (more than half an inch) of unnecessary voice-coil former length, providing the shortest possible distance between voice-coil winding and cone. Use of a low-loss rubber surround connected to the voice-coil former prevents interaction with the cone, while an open-fabric spider allows the cone to center in its underhung motor structure with higher linearity. The back surface of the driver is open, helping to eliminate reflections and unwanted energy storage. Accuton claims this new driver delivers a considerably more faithful response to an applied signal, and I find its contributions to play a significant role in the creation of this speaker’s unmistakably musical voice. This inventive driver covers the 250Hz to 2.2kHz bandwidth, offering remarkably flat response, again fed by a fourth-order acoustical G.A.I.N. circuit.
Von Schweikert Audio Ultra 9 Loudspeaker
Revelation
by Greg Weaver | Nov 14th, 2019
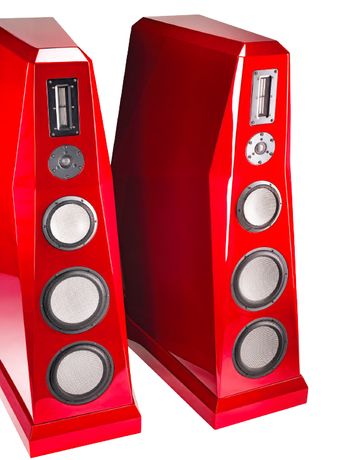
To understand the genesis of the new-generation VSA Ultra loudspeakers, we must go back to 2012, when a loyal, long-time VSA flagship owner contacted company founder Albert Von Schweikert and asked him to construct a one-of-a-kind, cost-no-object speaker. It will come as no surprise that Albert already had a theory for such a design, and this single project would overshadow everything, save standard production at VSA, for more than three years. Once Albert had settled on the drivers necessary for this ambitious project, Damon Von Schweikert, Albert’s son (and as of fall 2015 VSA’s CEO), spent a year on the enclosure alone. The overarching focus of this design was to reduce all forms of distortion, mechanical and electrical, to the lowest levels achievable. Even today, in any given system loudspeakers have the highest percentage of distortion of all components in the chain. (It’s unnerving to realize that even the most highly regarded speakers produce on the order of 3 to 5 percent distortion or more at their rated output.)
What would come to be known as the VR-111XS was housed in six separate enclosures, three per channel. Each channel included a nine-foot-tall concentric-array/line-source hybrid, housing eight magnesium 7" woofers, four magnesium 5" midrange drivers, two 1" horn-loaded magnesium dome tweeters, and an Air Motion Transformer super-tweeter, with an identical set of tweeters (two domes and an AMT), mounted in an ambient array on the rear baffle. The second nine-foot-tall tower housed four 12" magnesium subwoofers (with quad voice coils), each one powered by its own amplifier, while the third enclosure housed the impressive custom dividing network. All enclosures were fabricated with VSA’s proprietary “Triple-Wall Laminate Construction,” a unique constrained-layering technique utilizing three fundamentally different materials, each with vastly different “Q.”
The realization of this heroic loudspeaker would prove to be Albert’s swansong. As the finishing touches were being addressed in preparation for delivery and installation in mid-2015, he announced his retirement. This meant that Leif Swanson, Albert’s handpicked successor who has studied and worked with Albert for more than a decade, would assume the mantle of VSA’s head designer.
It was during the delivery and installation of this $750,000 statement design that Leif and Damon heard the VR-111XS in the customer’s purpose-built 25' by 75' by 16' room, and realized just how successful their three-and-a-half-year-long journey had been. Upon hearing how effectively they had achieved their desired goals with this speaker, the notion struck them both that they simply had to reimagine their entire flagship line. In November of 2015, the seed of what would become the Ultra line had germinated.
My impressions upon hearing the first speaker to result from this new initiative, the $300,000 Ultra 11 (which launched at AXPONA 2017), was that it represented a new benchmark, unmistakably surpassing the performance of every other speaker, regardless of price, that I had heard to that time. While some of the more competitive challengers offered remarkably diminished levels of distortion and perhaps even comparable degrees of resolution and transparency, in the areas of coherence, tone color, soundstaging, and especially dynamics the Ultra 11 simply had no equal.
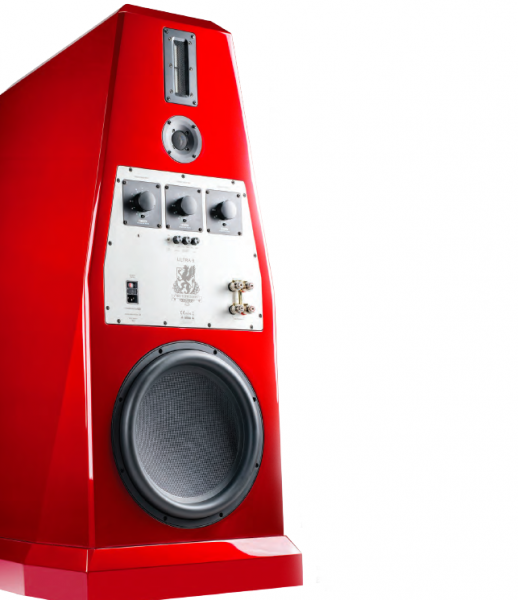
When I arrived at the Denver Marriott Tech Center before the opening of RMAF 2018, I was granted the singular privilege of getting a quick preview of the Ultra 9. What I had expected to find was simply a scaled-down version of the Ultra 11; after all, when comparing the two it is immediately apparent that the Ultra 9 is literally just the bottom half of an Ultra 11. But what I heard with the Ultra 9s being driven by Kevin Hayes’ then brand-new Valve Amplification Company Statement 450i iQ integrated amplifier (full review in progress) in this particular room and under the challenge of show conditions, was an entirely different, slightly more refined and involving speaker—one that in every way, save for the utter effortlessness and unrestricted dynamic scale of the Ultra 11, was as unfailingly authentic to the recorded event as its superb predecessor.
Getting in Tune
Seeing the Ultra 9 for the first time in its lustrous brilliant red finish is striking. Its multifaceted sides and angled front baffle give you the impression that it must be next to nightmarish to assemble. The fact that there are no right angles anywhere, nor any wider-than-necessary baffles to generate diffraction or interfere with dispersion, is also immediately evident. And weighing in at over 500 pounds and standing 50 inches tall, 32½ inches deep, with a 12-inch-wide front baffle (widening to a maximum width of 27 inches in the rear), this inspiring and massive device offers an amazingly streamlined and unimposing profile in every room where I have seen it installed, my own included. (My wife actually said, unprompted, “Those look amazing!”) Further, unlike many similarly sized speakers, the Ultra 9s are remarkably easily positioned on virtually any surface, with their rugged caster system, completely hidden by the purpose-built, form- and finish-matching skirt around the bottom of the enclosure.
The outermost layer of their proprietary triple-wall laminate composite enclosures consists of a sheet of resin-based HDF (high density fiberboard), a “medium” Q material, followed by a sheet of synthetic stone, fabricated from crushed gravel and various other minerals and a resin binder, with the third and innermost layer of hard felt (which has an extremely low “Q”), resulting in a wall some 4" thick. All three layers are bonded together using a layer (on the order of 1/5th of an inch), of industrial, anti-vibrational, plasticine-and-clay hybrid adhesive, integrating additional mechanical barriers capable of “shearing” energy by converting unwanted mechanical motion into heat for dissipation. Finally, using a method VSA has termed “Gradient Density Damping,” three different thicknesses of wool-like synthetic damping material are applied. Packed extremely tightly closest to the cabinet walls, the wool is gradually decreased in density as it nears the rear of the driver in its baffle, providing exceptional absorption while greatly reducing reflections back into the cone.
This inventive enclosure construction technique, known as “Aktive Cabinet Vibration Control, Version 2.0,” is the result of Albert’s extensive research using the California Institute of Technology’s (Caltech) Laser Interferometer Labs to study and measure speaker cabinet-wall vibration and the subsequent release of stored energy. It was pioneered and first applied in the original Von Schweikert Research VR-4, circa 1992.
While VSA readily acknowledges solid aluminum will be much more sonically inert than good ol’ HDF, they are quick to point out that this triple-walled, constrained-layer design results in sonic results measurably equivalent to and arguably even slightly more effective than milled aluminum. And it is radically more cost-effective. VSA feels that this method does not “squander” value, allowing the company to maximize the worth of the resultant product. This enclosure design technology has proven so successful that it is used in every VSA model in production today.
Lowest on the front baffle, the first two-thirds of which is swept back at about seven degrees, are two modified Accuton 8" honeycomb-ceramic drivers. Covering the 50 to 250Hz region and offering superbly flat response, they are fed from their fourth-order acoustical G.A.I.N. dividing network (more on that later). Though there is no low-frequency electrical filter, the explicit internal volume of the enclosure imposes a very steep acoustical roll-off below their lowest (50Hz) active frequency. Because they are not required to reproduce frequencies below 50Hz (there is a 15" subwoofer for that), these drivers exhibit an agility that results in both lower modulation and greater detail throughout their operational bandwidth.
Above the dual woofers, on that same swept-back section of baffle, is a unique Accuton 7" ceramic dome midrange. It implements an entirely new design approach Accuton calls the 4D (Direct Dome Drive Design) concept. As the spider is no longer connected to the former, its construction removes 15mm (more than half an inch) of unnecessary voice-coil former length, providing the shortest possible distance between voice-coil winding and cone. Use of a low-loss rubber surround connected to the voice-coil former prevents interaction with the cone, while an open-fabric spider allows the cone to center in its underhung motor structure with higher linearity. The back surface of the driver is open, helping to eliminate reflections and unwanted energy storage. Accuton claims this new driver delivers a considerably more faithful response to an applied signal, and I find its contributions to play a significant role in the creation of this speaker’s unmistakably musical voice. This inventive driver covers the 250Hz to 2.2kHz bandwidth, offering remarkably flat response, again fed by a fourth-order acoustical G.A.I.N. circuit.