Fellow members Madfloyd and Al M. came over this afternoon to listen to my system for the first time since the stay at home orders and general lock down have interrupted our visits. I have made many changes to the system since they had each been here, including the steel plate platforms on the rack, the XP-32, and the replacement of the Burley ICs and speaker cables with some custom signal cables made for me by Sound Concepts.
We played a variety of my LPs and some that Ian had brought with him. Ian has a great music collection, and I can always depend on him coming over with some LPs that I don't know and subsequently try to find for myself. We also compared the vdH Grand Cru on the SME 3012R arm to the MSL Signature Gold on the SME V-12 arm.
I think the general consensus was good. They remarked on the sheer amount of “detail” they heard. We disagreed on which arm/cartridge combination sounded more tonally correct, but we did seem to agree that the vdH conveyed more of the music's energy.
They preferred the presentation of the MSL Signature Gold on the V-12 arm. I preferred the vdH Grand Cru on the 3012R arm. I think they liked the warmer tonal balance and felt is was more timbrally correct, while I thought that combination was a bit warm and slightly soft sounding with slightly less energy.
I think of the vdH/3012R as cool clear bottle of water during a lovely afternoon sail. The MSL/V-12 is more like a warm bottle of Sake with a delicious sushi dinner. It is a matter of preference and taste.
I interpret their comments about detail to generally refer to the improved overall resolution of the system after all of the changes since they last heard it. They also remarked on the quality of the bass.
One of my goals this Spring, after I had already straightened my speakers and removed the acoustic treatments from the room to achieve what I consider a much more “natural” sound, was to increase the sense of “clarity”. As I mentioned before, the first adjective that comes to mind when I try to describe the sound at the BSO is “clarity”.
I became interested in the Pass Labs XP-32 after reading MAXPWR's report on his new preamp. We started to communicate and discuss how it differed from my XP-22. This led in turn to discussions about replacing my signal cables.
With the addition of the new preamp and cables, the sound is more clear and less grey allowing me to hear more of the energy from the music. There is simply less information lost in, or colored by, the chain of the system. Last Winter I removed the stuff from the system and room that was sucking the life and energy from the music and coloring the sound. My next step was to improve clarity. The preamp and cables do that. The system now more clearly conveys the energy captured in the grooves of my LPs, and that is why I think of it as "natural" sounding.
Ian and Al were the first people to hear the changes, and they seemed to confirm my own impressions. We had a fun little reunion and enjoyed a nice dinner outdoors at one of our favorite spots afterwards.
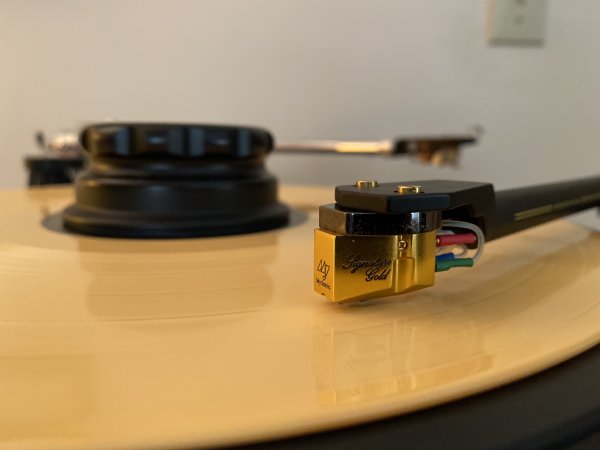