Hans Bristell Post Two
Entering in the 80’s changed my priorities. I attended Syn-Aud-Con hosted by Don Davis during a golden age of studio design technology. LEDE was the next development after Tom Hidley and the Westlake period, with 800+ studios built around the world. Synergetic-Audio-Concept opened new doors by meeting with the world class studio engineers and acoustic designers. This experience and meeting creative people, changed the attendees' view as we shared our knowledge, forming a new world class of studio engineers. Don Davis was the hub in Syn-Aud-Con classes. Around 1979 Chips and Don Davis introduced a new studio design concept, LEDE (Live End Dead End). The list of talented people that was teaching the classes was impressive.
Richard Heiser, a NASA scientist and inventor of TEF (Time Energy Frequency), introduced a revolution in our understanding of studio acoustics by waterfall graphic presentation. Peter D’Antonio was a diffusion expert at Syn-Aud-Con classes. His mentor was Manfred Schroeder at Bell Laboratories. Peter commercialized the Schroeder diffusor in his company RPG diffusor. Doug Jones was a spokesperson for the deceased Paddy Rodgers, on her PhD thesis of the pinna effect / HRTF (Head Related Transfer Function).
The inventor of RFZ (Reflexion Free Zone), Charles Billelo, introduced his most famous RFZ design Master Sound Astoria. The hands-on of studio design was taught by Russell Berger of Joiner Rose Group, a studio designer company. This is just a fraction of the shared knowledge.
This opened a new world for most attendees and increased my understanding of the studio and acoustic technology. This new knowledge effected my studio design in a profound way. I was assigned at Swedish Television to build the first certified LEDE control room in northern Europe in the 80’s, followed by the first 5:1 surround sound mix room in Scandinavia. After establishing my own company I built a state of the art mobile control room, followed by a multi-studio complex for Walt Disney's Swedish productions. In the late 80’s I was involved in a opera studio in the country owned by Håkan Hagegård, a Swedish opera singer.
This lead to the project I would like to share, about my infrasonic bass horn control-room. It was a novel control room where I used all my knowledge learned at Syn-Aud-Con classes. It was based on LEDE by Don Davis and combined with RFZ by the deceased Charles Billelo. The control room was divided into two frequency ranges, the geometric acoustics and the wave acoustics - both are divided by the transition frequency (Schroeder frequency) of the room.
Wave acoustics was reproduced by a infrasonic horn. The horn was divided in three parts. The first tractrix horn part was hidden under the floor, and the second part was folded in the front of the control room. The third part was the extension of the horn forming the control room conical extension. (See below sketch). The calculation of the horn was done by David Shuttric, a mathematician and horn designer from England.
This was a demanding project. You have to combine the LEDE and RFZ geometric design with a infrasonic horn integrated in the control room.
It was a challenging construction, but well rewarded with an outstanding result.
I supposed it was the first infrasonic control room designed as a sub-bass horn.
The benefit of this design is to integrate the horn and the room to one acoustic transformer. The connection of a sub-bass horn into a regular room has been investigated in one AES paper by Björn Kolbrek. It was presented at the 146th Convention from 20-23 March, 2019 in Dublin, Ireland. The subject was Large Horns and small room - Do They Play Nicely Together?.
This is an independent view of my design to connect and integrate the horn in the room. This paper shows how the standing waves in the room create a variation on the room impedance connected to the mouth of the horn. The room should have as smooth distribution of standing waves as possible, to present a low impedance to the horn mouth. This reduces the back wave into the horn that reduces the standing wave inside the horn.
This results in a smoother frequency response from the horn. The connection of the horn mouth at the rear of the room was to a room with a volume of 4000m3. This volume presents an reasonable acoustic impedance to the horn mouth that was the rear end of the control room. This was not a free-field condition, but very close. The drawing and the hi-res pictures were unfortunately stolen.
I have made sketches of the room, from my memory of the drawings. I have saved some pictures that are low resolution that I can share with you. It is the construction of the first part of the tractrix horn, and the folding part of the front of the room and when the carpenter finished the floor on top of the first part of the horn. The room was designed as a conical expansion of the rear of the room.
The back of the room was acoustically open to the 4000m3 open space simulating a free field with standing waves down in the 10Hz range. The horn used some resistance to attenuate the possible standing waves inside the acoustic transformer. This was an invention by Gedlee used in their NS15 mid-horn design. The transducer in the throat end is a custom 15-inch woofer designed for infrasonic horn. It has a magnetic force of 2 Tesla, the same as in my horn in Post 1!. The ratio between the area of the throat, 315cm2 and the Mouth area, 25m2 (25000cm2) is a acoustic ratio of 25000/315 = 80:1. This is a good match of the acoustic transformer. I don’t know the metrics for this design. The floor plan is 35m2 and the dimension is 7x6x4 meters. This is a model of a full-size control room built in dry material.
The Brivox full size control room is twice the volume and the length of the horn is 25m. The shell and the horn are built in acoustacret, a proprietary material by Brivox. This material is working as a viscoelastic material with controlled weight, reducing structure born sound and improving the soundproofing of the studio. When building to a full-size scale of 70m2 of the Brivox Infrasonic room and using infrasonic horn, this should be built in acoustacret.
To compare to BOP, a studio built by Tom hidley in South Africa, the studio outer walls are built in concrete and a inner shell of dry material. The control rooms are infrasonic rooms with direct-radiating subwoofers 4x18 inch transducers in one box. The rooms are heavily dampened in the Wave acoustic range. The room size is about 70m2 and a unique future is there is an under the floor space with wave acoustic trap. The acoustics in the geometric range are non-environment acoustics mimicking a free field situation. The broadband RT curve has a very low value (close to free field). See below drawings of BOP Studio.
Concerning the infrasonic wave acoustics in the Brivox control room, I have no metrics to show more than a broadband RT curve close to 0.3 seconds. But I can tell you how my body reacts. First reaction was that my body was resonating around 7Hz and the SPL level was extremely high (130dB SPL). When your body begins to vibrate your inner organs are vibrating as well. It is a very uncomfortable experience.
The lungs are vibrating around 7Hz; when you talk the voice is frequency modulated in a way that is hard to understand what you are saying. Your eye globes vibrate, which causes double- vision, very scary. You begin to feel nauseous because your brain and inner ear are vibrating. If the SPL is increased, it can result in heart failure. This is the limiting factors listening to a infrasonic horn of this magnitude. If you ask me if the SPL and frequency range is good enough, I can give you the same answer that a customer to a Rolls Royce car was asking, "how many horsepower does the engine has”, and the answer was "more than enough.” I can give the same answer concerning the SPL and frequency range of this infrasonic control room, then it is 'more than needed.
Some comments about the geometric acoustics are a differentiator compared to BOP studio NEA (Non Environment Acoustics) after Wilhelm Lassen Jordan. In a Brivox LEDE room, a 10 inch wedge foam was used to control the earlyreflexions in the front of the LEDE room. The wedges have the double function to attenuate the higher order frequencies in the second folding part. At the rear of the room diffusors was used, i.e. golden horn that shattered the discrete reflexes to create a diffused transparent sound field at the back of the room. The side of the room I used what Charles Billelo called RFZ. He used mirrors to steer the discrete reflexes outside the sweet spot. This is the reflexion-free Zone (see below drawings). As an alternative, a Acrylic Wing can be used to diffuse the side wall window reflexions. Wing (nearfield broadband temporal diffusion) is what I refer to as the novel diffusor invented by Matts Odemalm at SMT Sweden. The Wing concept will be used in my ongoing project of Brivox studios.
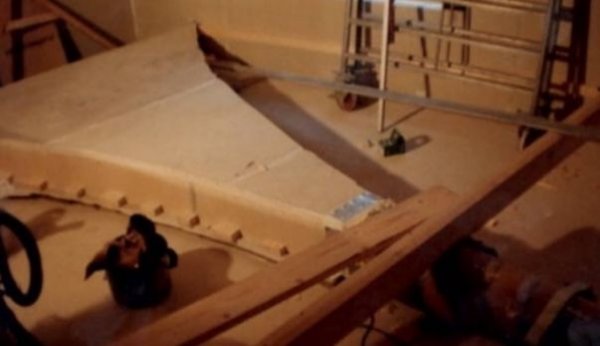
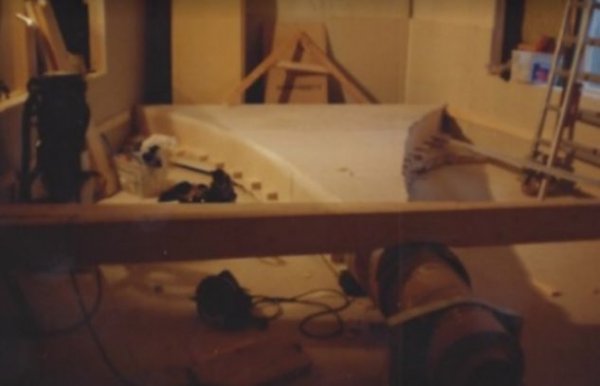
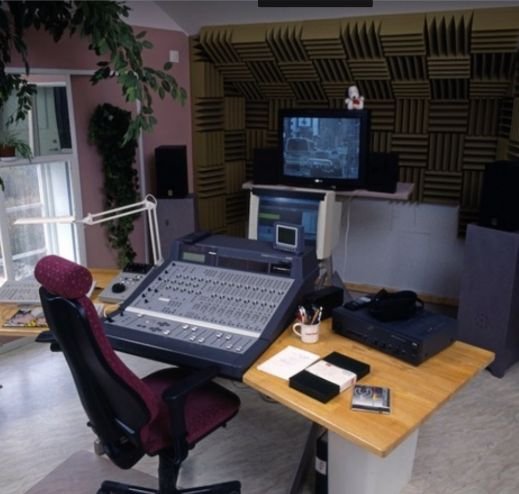
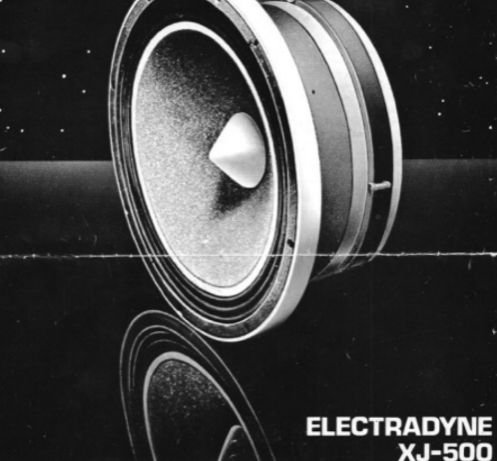
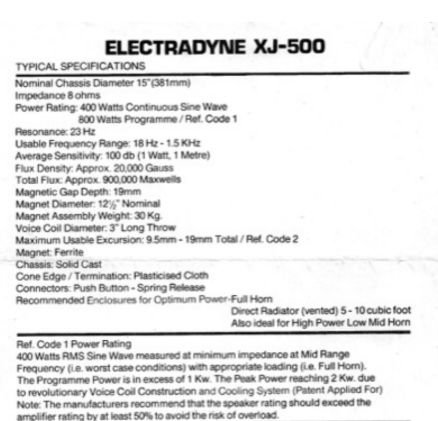
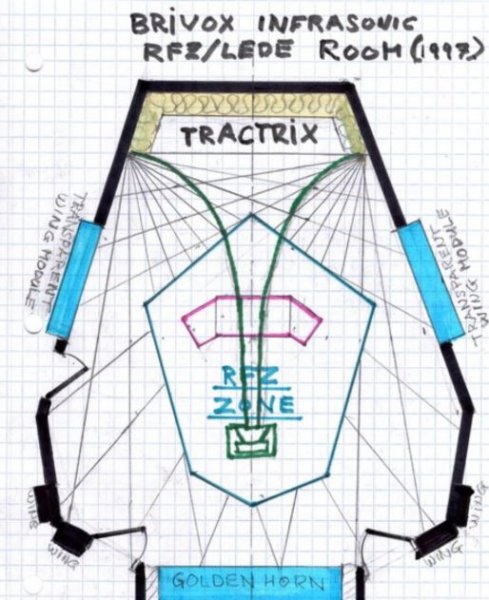
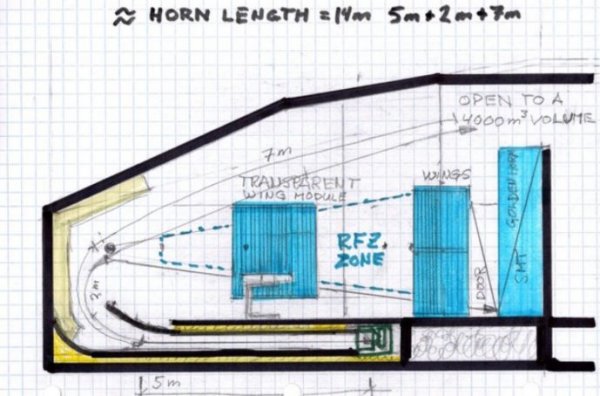
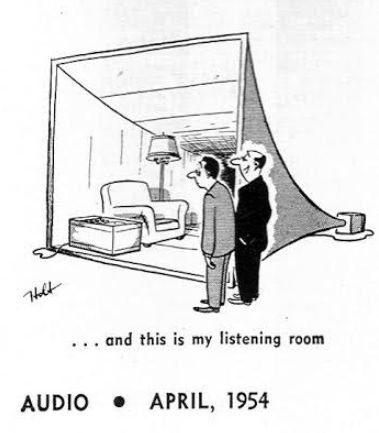